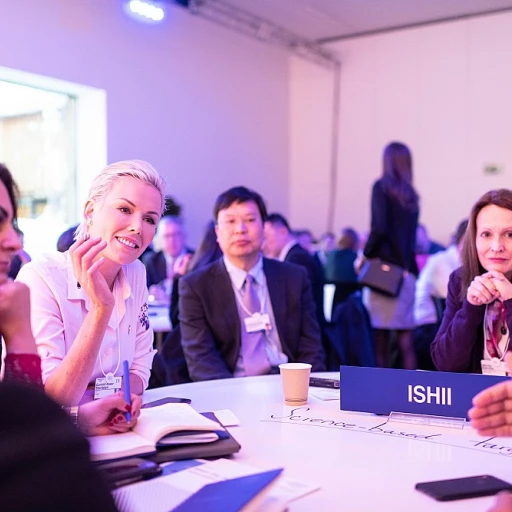
Understanding the Core Principles of Kaizen and Six Sigma
The Essence of Kaizen and Six Sigma
To appreciate the significant impact of Kaizen and Six Sigma in change management, it's crucial to delve into their core principles. Both methodologies share a common goal: continuous improvement by focusing on minimizing waste and enhancing quality. However, they approach this goal differently, providing organizations with a rich set of tools to achieve operational excellence.
Kaizen, a Japanese term meaning "change for better," emphasizes small, consistent improvements involving the entire organization. It nurtures a culture of continuous improvement that encourages every team member, fostering a collaborative work environment aimed at enhancing customer satisfaction. Through kaizen events and kaizen training, organizations can drive progressive changes essential for sustainable growth.
On the other hand, Six Sigma employs a rigorous, data-driven approach to eliminate defects and reduce variations in processes. By adhering to a set of statistical tools and techniques, Six Sigma aims to improve the quality of project outcomes. Its hierarchical project management certification levels, such as Green Belt and Black Belt, empower team members to lead quality improvement initiatives effectively.
Comparing Key Methodologies
While both Kaizen and Six Sigma revolve around process improvement, they represent distinct philosophies within the realm of quality management. Kaizen's strength lies in its flexibility and capacity to integrate into daily operations. It's about nurturing a continuous improvement mindset and identifying processes that could benefit from frequent refinements.
Conversely, Six Sigma's power is rooted in its precision. It employs a structured framework that quantifies the impact of changes on quality and efficiency, ensuring that each sigma project aligns with strategic business objectives. By implementing these methodologies, organizations are better equipped to achieve unparalleled efficiency and superior quality outputs. Understanding the synergy of Kaizen and Six Sigma, can unlock potential in business process management.
The Synergy Between Kaizen and Six Sigma
The Harmonic Collaboration of Continuous Improvement Methodologies
While examining the realms of continuous improvement, it becomes essential to explore the synergy between Kaizen and Six Sigma. These methodologies, when intertwined, harness a powerful blend of lean thinking, problem-solving techniques, and quality management, paving the way for remarkable operational excellence. At its essence, Kaizen promotes a culture of continuous process improvement. It's an approach fueled by small, incremental changes that collectively enhance the efficiency of processes. On the other hand, Six Sigma, with its data-driven methodology, seeks substantial quality improvements through meticulous elimination of waste and meticulous sigma projects. Both are geared toward customer satisfaction and achieving organizational business objectives. Despite sharing common ultimate goals, there are key differences between these approaches. Kaizen lays its roots in cultivating a vibrant team culture where all team members are stakeholders in the process improvement journey. Six Sigma, meanwhile, adopts a structured, analytical approach focused on eliminating defects and variations in processes. Nevertheless, when these methods converge, the resultant lean sigma strategy synergizes process improvement with rigorous statistical analysis, empowering organizations to accelerate project management with profound efficiency. The strategic fusion of these methodologies not only facilitates the enhancement of internal processes but also contributes to the development of an adaptable and resilient organization. A robust synergy between Kaizen and Six Sigma can effectively address challenges that arise in business dynamics, often highlighted during Kaizen events or sigma lean activities. Through collaborative Kaizen training and Sigma certification programs, businesses are better positioned to foster a thriving environment of problem solving and eliminating waste. Discover more insights on this topic by exploring our discussion on unraveling problem-solving and understanding the common causes of failure in change management. This seamlessly integrates the core principles of Kaizen sigma, guiding organizations in maneuvering through challenges with adept precision.Implementing Kaizen and Six Sigma in Organizational Change
Integrating Kaizen and Six Sigma into Your Organization
Implementing Kaizen and Six Sigma in an organization requires more than just understanding their individual principles; it demands a synergistic approach. To drive significant continuous improvement and ensure operational excellence, it's crucial to blend these methodologies seamlessly into the fabric of the organization’s culture.
Establishing the Foundation for Effective Implementation
Before initiating any transformation project, it is essential to ensure that the team is well-prepared. This involves comprehensive Kaizen training and Six Sigma certification programs. Such initiatives will equip team members with the necessary problem-solving tools and techniques, fostering a culture of quality management and continuous improvement. An investment in black belt certification can significantly enhance the expertise needed for complex sigma projects.
Creating a Collaborative Environment for Change
Successful process improvement hinges on collaboration. Encourage the formation of cross-functional teams to ensure diverse perspectives and skill sets contribute to the change process. Organize regular kaizen events to engage employees from different levels of the organization, which not only facilitates lean sigma processes but also boosts customer satisfaction and aligns with business objectives.
Emphasizing Data-Driven Decision Making
A key aspect of the Kaizen Six Sigma approach is its reliance on data-driven methods. Utilize statistical tools and process mapping techniques to identify inefficiencies. These insights will drive process improvements by eliminating waste and enhancing quality. This data-centric approach empowers team members to make informed decisions, thereby accelerating the pace of change.
Aligning Change Initiatives with Strategic Goals
Ensure that all initiatives are aligned with the organization’s strategic goals. This alignment not only enhances customer satisfaction but also prioritizes projects that contribute directly to business value. Engage in regular project management reviews to track progress and make necessary adjustments, ensuring that improvement efforts remain on target and deliver expected outcomes.
Overcoming Challenges in Kaizen Six Sigma Adoption
Addressing the Hurdles in Kaizen and Six Sigma Integration
Incorporating Kaizen and Six Sigma methodologies within an organization's change management strategy can be a game-changer, promoting continuous improvement and operational excellence. However, the journey is not without its hurdles. Understanding and overcoming these challenges is crucial to ensuring effective integration.One of the most significant challenges is cultural adaptation. Both Kaizen and Six Sigma require a shift in organizational culture toward continuous improvement and data-driven decision-making. This shift can be met with resistance, especially if team members view it as a threat to established processes. Developing a culture that embraces change and values employee input is vital to its success. Conducting regular kaizen events can serve as a helpful tool in adjusting mindset shifts and enhancing team cohesion.
Training and certification form another critical aspect to tackle. To effectively implement Kaizen and Six Sigma, organizations must invest in comprehensive training for their staff. This includes educating team members on tools and techniques, as well as fostering a shared understanding of the Lean Sigma principles. Offering incentives for kaizen training and recognizing achievements such as becoming a Six Sigma Black Belt can motivate employees to engage with the change initiative.
Project management poses another obstacle. Managing Kaizen and Six Sigma projects requires careful coordination and monitoring. Establishing clear objectives, assigning specific roles, and employing robust project management methodologies can help in keeping improvement processes on track. Frequent communication and feedback loops enable teams to address issues promptly and align with the core goal of increasing customer satisfaction.
Moreover, effectively managing time is crucial. The implementation processes can be time-intensive, emphasizing the importance of setting realistic timelines and milestones. It’s essential to balance process improvement activities with day-to-day operations to prevent overload and disengagement among staff.
Lastly, to foster long-term success, it is vital to maintain momentum and avoid complacency. Organizations should foster a relentless pursuit of quality management and problem-solving to ensure that the benefits of Sigma and Kaizen are sustained over time. This proactive approach will ensure that businesses continue to eliminate waste and drive continuous improvement long after the initial stages of implementation.
Successfully integrating both methodologies requires a strategic approach and commitment to overcoming challenges. As organizations embrace this dual approach, they streamline processes and add significant value, ultimately leading to increased customer satisfaction and business growth.
Measuring Success: Metrics and KPIs for Kaizen Six Sigma
Assessing the Impact of Lean Sigma on Continuous Improvement
Accurate measurement of success in implementing kaizen and Six Sigma is vital for ensuring that the desired improvements actually occur. To achieve this, organizations employ various metrics and KPIs that provide data-driven insights into the effectiveness of their change management efforts.- Improvement Metrics: The primary goal is to enhance process efficiency. Metrics such as cycle time reduction, increased throughput, and defect rate reduction offer tangible evidence of improvements in operational excellence.
- Customer Satisfaction: Enhanced quality management processes should translate to better customer satisfaction. Tools like customer surveys and Net Promoter Scores (NPS) provide valuable feedback on customer experiences following a sigma kaizen project.
- Cost Reduction: Financial metrics are crucial in determining ROI. Lean sigma initiatives often focus on eliminating waste, leading to direct cost savings and increased profitability.
- Process Improvement: Tracking process metrics, such as lead time and waste reduction, shows the organization's capability to implement effective kaizen events and sigma projects, highlighting successful process improvements.
- Project and Time Management: Efficient project management and effective use of team members' time are measurable through adherence to project timelines, budget adherence, and resource utilization. Black belt certified members typically lead these efforts.
Real-World Examples of Kaizen and Six Sigma in Action
Showcasing Operational Excellence
In the realm of organizational change, numerous companies have successfully adopted Kaizen and Six Sigma methodologies, leading to continuous improvement and enhanced quality management. These real-world examples demonstrate not only the theoretical benefits but also the tangible impact on business processes and customer satisfaction.
One notable example involves a global manufacturing company that utilized Kaizen events to foster a culture of continuous improvement. By empowering team members to identify and eliminate waste, the company significantly reduced lead times and enhanced process efficiency. The emphasis was on operational excellence and problem solving, aligning with the Kaizen philosophy of small, incremental improvements.
Data-Driven Decision Making in Healthcare
The healthcare industry has also seen remarkable improvements through the integration of Six Sigma and Lean Sigma methodologies. A prominent healthcare provider implemented Sigma projects to address issues in patient care processes. By leveraging data-driven tools and adopting a systematic approach to process improvement, they not only enhanced the quality of care but also increased patient satisfaction.
Through Kaizen training and Lean Sigma certification for their staff, the organization was able to cultivate a team management culture focused on reducing errors and streamlining operations. This approach not only improved customer outcomes but also demonstrated the importance of structured training in achieving long-term success.
Transforming Service Industries
In the service industry, a leading financial institution adopted the Kaizen Sigma methodologies to optimize its project management processes. Focusing on eliminating waste and enhancing service delivery times, the organization embarked on a series of Kaizen events. By employing Lean principles, they were able to align their services more closely with customer needs, achieving superior quality management outcomes.
Through a collaborative effort involving all team members, the institution saw significant improvements in efficiency and customer satisfaction. The success of this approach underscores the importance of creating a continuous improvement mindset within the organization.
These examples illustrate that the implementation of Kaizen and Six Sigma is not confined to one industry or sector. Rather, these methodologies offer a versatile approach for any organization seeking to achieve operational excellence and maintain competitiveness in a dynamic business environment.