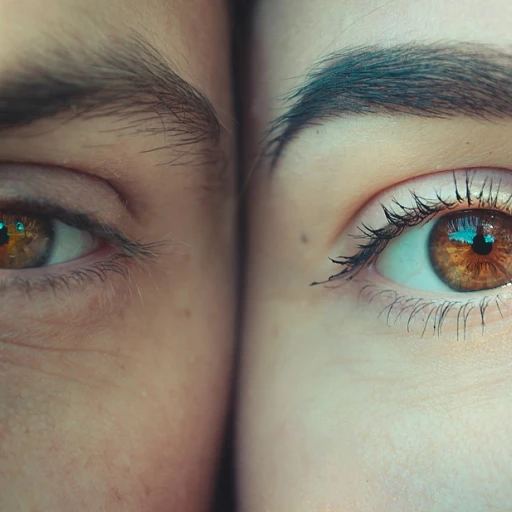
Understanding Statistical Process Control
Exploring the Fundamentals of SPC
Understanding Statistical Process Control (SPC) is crucial for any organization aiming to enhance their quality management systems. This methodology involves using statistical techniques to monitor and control a process to ensure it operates at its full potential. At the core of SPC are control charts, which are pivotal tools used to visualize data over time. SPC goes beyond mere data collection; it focuses on process capability and the use of control charts to interpret SPC data. These tools help identify variations in a process and are essential for quality control initiatives. When process variations are detected, SPC techniques are employed to determine if these variations are due to common causes or indicative of a significant change in the process. Implementing SPC requires a comprehensive understanding of control limits and the ability to interpret SPC charts. This knowledge is often supplemented through programs like SPC training courses, which are available both in-person and online. These courses will typically explain how to effectively use control SPC and develop a robust process control strategy, building towards quality management and continuous improvement. For professionals, especially those targeting a sigma black belt certification, the insights gained from SPC courses and control training can be invaluable. Participants will learn crucial skills such as data analysis, problem-solving using statistical methods, and evaluating process capability. These courses not only provide theoretical knowledge but often include practical content like video tutorials that help consolidate learning. Moreover, organizations need specialized SPC training to overcome specific challenges in implementing training programs. Mastery of these statistical methods can lead to significant improvements in process quality and efficiency. By investing in quality SPC training, businesses can harness the power of statistical process control to enhance their operational capabilities. For a deeper dive into maximizing workforce potential, consider exploring total talent management strategies here.The Role of Training in Change Management
The Influence of Comprehensive Learning Modules
In the realm of change management, training plays a critical role in guiding organizations through transitions.
Improving process control through Statistical Process Control (SPC) training ensures that employees are equipped with the necessary control techniques and quality management strategies. The ability to interpret control charts and understand process capability is vital for maintaining quality control during organizational changes. SPC courses extensively cover these aspects, offering employees not just knowledge, but practical expertise.
The structure of SPC training includes both theoretical learning and practical application, often encompassing video content, online modules, and in-person workshops. Companies invest in these courses to provide their teams with tools for accurate data collection and analysis, a step crucial for informed decision-making.
- The program will help staff understand control limits and the significance of Sigma Black Belt methods.
- Employees receiving SPC data and control training become adept at using SPC charts, enhancing the organization’s operational efficiency.
- Quality control through SPC training ensures that processes remain stable over time, a pillar in effective change management.
Continuous learning through these programs—integrating modern digital methods like video course content—ensures that personnel remain updated with the latest SPC techniques. Organizations recognize that quality management and control SPC training significantly impact process control and, consequently, the success of any change management initiative.
Key Benefits of Statistical Process Control Training
Advantages of SPC Training on Effective Change Management
Statistical Process Control (SPC) training equips teams with the necessary skills to harness data effectively, which is essential for quality management during change processes. By mastering control charts and process capability analysis, individuals can gain a clearer understanding of process variations and the impact of changes. This training empowers employees to make data-driven decisions, reducing the guesswork in quality control. With SPC training, participants learn to:- Employ Control Charts: Gain expertise in creating and interpreting control charts that help in monitoring process stability and identifying trends before they become issues.
- Enhance Process Capability: Analyze and improve the process capability, allowing teams to understand better the processes' performance within specified control limits.
- Implement Effective Data Collection: Training often includes methods for robust data collection, vital for maintaining the integrity and accuracy of SPC data, leading to more insightful analyses.
- Adapt SPC Techniques: Trainees explore various SPC techniques that can be applied to both short and long-term projects. This adaptability is crucial in a dynamic work environment.
- Prepare for Certification: Many SPC training programs culminate in certification, such as the sigma black belt, signifying a high level of competence and enhancing the value participants bring to their organizations.
Challenges in Implementing Training Programs
Navigating the Complexities of Program Implementation
Implementing training programs in the realm of Statistical Process Control (SPC) comes with its unique set of challenges. The integration of control mechanisms, statistical techniques, and quality charts demands a comprehensive approach to learning and application. When embarking on SPC training initiatives, organizations often encounter hurdles that need strategic solutions. One of the primary challenges is the diversity in learning needs across the workforce. Courses must cater to various expertise levels, from novices to those seeking a black belt in SPC techniques. Designing a program that balances foundational concepts of control charts and advanced process capability methods is crucial for effective skill enhancement. Time is another critical factor. Employees often juggle multiple responsibilities, making it difficult to allocate consistent hours to an extensive spc training schedule. Balancing workload with education requires flexible learning methods, such as online video content, which allows participants to learn at their own pace while maintaining productivity. Data collection and interpretation also pose significant obstacles. Individuals must develop proficiency in analyzing SPC data and deciphering control limits within quality management contexts. Specialized courses focusing on these areas ensure that trainees not only understand theoretical aspects but can also apply them practically in real-time situations. Moreover, keeping participants motivated throughout the control training journey can be challenging. Offering interactive badges and certifications can serve as incentives, recognizing advancements and sustaining momentum. This approach builds a culture of continuous improvement, aligning with overarching quality control objectives. Ultimately, the facilitation of effective training programs hinges on robust process control and tailored course content that resonates with diverse learners. Organizations can overcome these challenges by devising strategic solutions aligned with their specific needs and goals in statistical process enhancement.Best Practices for Effective Training
Best Approaches for Effective Learning and Implementation
To truly harness the benefits of Statistical Process Control (SPC) training, organizations must adopt strategic approaches that facilitate effective learning and seamless implementation. This task isn't merely about beginning a training course but involves a nuanced understanding of both human and technical aspects.- Choose the Right Program and Content: Selecting a suitable SPC training program is crucial. Depending on the needs, this could range from basic courses covering SPC charts and process control to advanced ones focusing on control limits and sigma black belt certification. Tailored programs that address specific quality control challenges provide more value and ensure relevance.
- Incorporate Various Learning Formats: Offering a mix of in-person and online training options, such as video tutorials and interactive online modules, caters to different learning preferences. This flexibility enhances engagement and allows participants to learn at their own pace, optimizing retention and application of knowledge.
- Leverage Data and Control Charts: Integrating practical exercises with real data collection and control SPC charts not only helps in understanding statistical methods but also in appreciating their real-world application. This practical approach bridges theory with practice, reinforcing the utility of SPC data in driving quality improvements.
- Engage with Expertise and Authority: Involving seasoned instructors, perhaps those with a background in black belt certification or extensive experience in quality management, adds a layer of credibility. Their insights into process capability and control training enrich the learning experience and foster a culture of continuous improvement.
- Foster an Ongoing Learning Environment: Establishing a culture where learning is continuous encourages participants to refine their skills over time. This mindset is crucial for sustaining long-term improvements. Offering advanced modules or refreshers ensures that employees remain proficient and adaptable to new methodologies.
Case Studies: Success Stories
Real-Life Examples of Successful Implementation
- Manufacturing Giant's Transformation: One notable case involves a leading manufacturing company that embraced SPC techniques. By enrolling their team in an SPC training program, the company improved its process capability and quality management significantly. The training, structured over a series of in-depth courses, covered topics such as control charts, data collection, and control limits. As a result, the company's operational efficiency soared, and they achieved an enviable level of product quality. With the acquired skills, team members earned a black belt certification, showcasing their proficiency in statistical process control.
- Pharmaceutical Firm Boosting Quality Assurance: Another example is a pharmaceutical company's journey towards quality excellence. Faced with increasing demands from regulatory bodies, the firm opted for SPC training to fine-tune their process control systems. This program helped in honing employees' abilities to use statistical data effectively, thereby enhancing quality control processes. The company's commitment to quality was evident as they utilized SPC charts and control spc methods extensively. The short spc course played a crucial role in swiftly upgrading the skill set of their workforce.
- Automotive Sector Enhancing Production Lines: The automotive industry also provides a compelling example where an organization utilized online training courses to roll out SPC improvements across their production lines. This flexible training format allowed employees to engage with content through video lessons, optimizing their learning time and enabling them to apply newly acquired SPC data skills to real-world challenges. The initiative resulted in a notable increase in process efficiency and product quality, ultimately leading to substantial cost savings.
These cases underscore the potency of well-structured training programs in executing change management and improving organizational performance. By equipping staff with vital skills in statistical process control, companies not only enhance their process capability but also embed a culture of continuous improvement. This, in turn, aligns with quality management objectives, ensuring sustainable growth and competitive advantage.