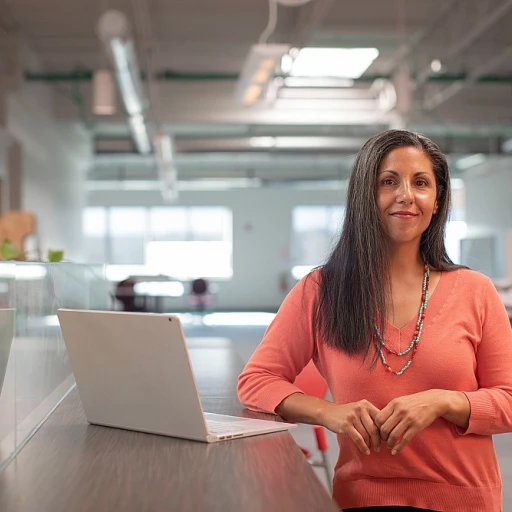
Understanding Non-Essential Tasks
Discerning Necessary from Non-Essential
Understanding the distinction between necessary and non-essential tasks in change management is crucial for any organization seeking to enhance its processes. It involves an emphasis on tasks that add true value to the final product or service and contribute to customer satisfaction. These value-added activities are the foundation of a lean approach, which focuses on maximizing customer value by minimizing waste and ensuring every step in the process adds value. To streamline your processes, it's essential to identify activities that do not directly contribute to the end product or customer satisfaction. These non-value added tasks can consume resources, time, and energy without providing any benefit to the customer, hence not warranting a customer's pay. Reducing these non-essential tasks aligns with lean sigma principles, which advocate for efficiency, quality improvement, and continuous advancement in business operations. By focusing on value-producing actions, organizations enhance their processes, leading to improved product service and better alignment with customer expectations. For businesses looking to refine their change management strategies, focusing on these aspects can reduce inefficiencies and lead to a measurable improvement in results. To dive deeper and craft an effective project management plan, read more about strategic planning methodologies.Identifying Non-Value Added Activities
Recognizing Non-Value Activities
In the realm of change management, identifying activities that do not add value to the end product or service is crucial. These tasks, often classified as non-value added (NVA) activities, do not contribute to the customer's satisfaction or improve the final output.
The first step in distinguishing NVA activities is understanding what the customer is willing to pay for. By focusing on activities that directly impact the quality and effectiveness of a product or service, organizations can streamline processes and reduce waste. This approach aligns with lean methodologies, which emphasize efficiency and the elimination of wasteful steps in any process.
Consider a typical supply chain process: it includes multiple stages, and each stage needs to be scrutinized for its value contribution. Some activities, while necessary, might not add direct customer value and can be considered for modification or elimination. The goal is to remove redundant steps that soak up time and resources unnecessarily.
Utilizing lean sigma techniques can help in identifying these NVA tasks by analyzing processes for waste and inefficiency. Businesses can employ tools, like process mapping and value stream analysis, to visualize all steps involved in workflows and zero in on those that do not add value. By reducing nva activities, companies not only enhance efficiency but also improve customer value, leading to better overall quality and satisfaction.
Impact of Non-Essential Tasks on Change Management
Effects of Non-Essential Tasks on Efficiency
Non-essential tasks within a change management framework can detrimentally impact both efficiency and overall organizational productivity. By focusing resources on activities that do not add value, businesses risk wasting time and reducing the effectiveness of their change management efforts. Understanding this impact is crucial for implementing effective strategies. Engaging in non-value added activities can lead to resource drain, where time and effort are consumed by processes that don't directly contribute to the customer experience or improve product service quality. These activities often lack the value adding component that is crucial for customer satisfaction and business improvement. This not only affects the supply chain but also delays steps in the process that can enhance overall efficiency. Such inefficiencies can lead to unnecessary waste—both in terms of time and resources. The ultimate consequence is a slowdown in continuous improvement efforts and a hindrance to business growth. By identifying and eliminating these tasks, organizations can ensure that their focus remains on value-added activities, thereby unlocking the potential for increased productivity and quality improvement. Through Lean Six Sigma practices, companies can assess their current processes and recognize non-value added tasks. Lean sigma methodologies offer techniques to streamline processes, ensuring all activities directly contribute to value added goals. This approach positions businesses to focus on enhancing processes that yield high customer value, which is crucial in delivering results that customers are willing to pay for and increasing customer value perception. Considering the detrimental effects of non-essential tasks, it is pertinent for organizations to constantly review and optimize their operations. For more insights on crafting change management methodologies that eliminate waste, explore this comprehensive guide on the ADKAR Model for Effective Change Management. This resource provides valuable steps to integrate efficient strategies into your change processes effectively.Strategies for Eliminating Non-Essential Tasks
Methods for Reducing Inessential Steps
In the quest for successful change management, it's imperative to focus on reducing non-essential tasks that contribute little to no value. Streamlining business processes begins with understanding which activities add value and which simply consume time and resources without enhancing customer satisfaction or product/service quality. Eliminating non-value added activities involves a strategic approach to create a more efficient workflow. Consider the following steps:- Adopt Lean Principles: Lean methodology is central to identifying inefficiencies. By implementing Lean principles, companies can minimize waste within processes, enhance efficiency, and increase value added to the customer.
- Apply Lean Sigma Techniques: Lean Sigma combines Lean's focus on waste reduction with Six Sigma's emphasis on quality improvement. This hybrid approach can reduce process variations and eliminate inefficiencies that don't enhance customer value.
- Evaluate Process Efficiency: Conduct regular audits to assess which nva activities detract from the core business objectives. Understanding these aspects will guide efforts towards value adding and streamline operations effectively.
- Cross-functional Teams: Encourage collaboration across different departments. Teams composed of diverse skill sets can provide comprehensive insights into which activities directly add value to the process and which should be modified or eliminated.
- Continuous Improvement Initiatives: Establish a culture of ongoing improvement. Encouraging feedback and innovative ideas from employees can drive process enhancements and boost both efficiency and value product delivery.
Tools and Techniques for Streamlining Processes
Streamlining Processes with Tools and Techniques
In change management, eliminating non-essential tasks is crucial for enhancing efficiency, improving quality, and adding value to the entire process. Leveraging the right tools and techniques can help streamline processes effectively, enhancing customer satisfaction and reducing waste. One of the popular methodologies for streamlining is implementing Lean principles. Lean focuses on waste reduction, ensuring every activity adds value directly to the customer. By identifying and minimizing non-value added activities, businesses can concentrate on what truly matters – maximizing customer value and optimizing resources. For companies looking to adopt this approach, a Lean Sigma framework can be beneficial. Combining Lean methods with Six Sigma techniques helps in continuous improvement, focusing on quality enhancements and reducing variability in processes. This method provides a structured approach through defined steps that guide businesses toward efficiency and value-added processes. Moreover, investing in technology solutions for process automation can significantly influence time management and resource allocation. Automation tools reduce manual tasks, streamline communication, and facilitate the flow of information across the supply chain. This approach not only saves time but also minimizes the potential for human error, enhancing overall productivity. Business process management software is another strategic tool to consider. These platforms offer dashboards, real-time analysis, and process mapping, giving managers insights into every business operation, pinpointing non-essential activities and enabling timely interventions. Incorporating these tools and techniques in change management leads to a more efficient, effective, and value-driven business environment, ensuring that each product and service meets the high expectations of customers and adds tangible value.Case Studies: Successful Change Management
Real-World Examples of Streamlined Change Management
In the realm of change management, eliminating non-essential tasks can significantly enhance efficiency and customer satisfaction. Here, we explore some real-world examples where businesses have successfully streamlined their processes to add value and improve quality.
Case Study 1: Lean Sigma in Manufacturing
A leading manufacturing company implemented Lean Sigma methodologies to identify and eliminate non-value added activities in their production line. By focusing on value adding steps, they reduced waste and improved product quality. This not only enhanced customer satisfaction but also optimized resource allocation, leading to a more efficient supply chain.
Case Study 2: Service Industry Transformation
In the service sector, a prominent company re-evaluated its processes to remove activities directly impacting customer service negatively. By streamlining their workflow, they reduced the time taken to deliver services, thereby increasing customer value. This continuous improvement approach ensured that only value added activities were prioritized, enhancing the overall business efficiency.
Case Study 3: Digital Transformation in Retail
A retail giant embraced digital tools to eliminate non-essential tasks in their online operations. By leveraging technology, they improved their product service delivery, ensuring that every step in the process added value to the customer. This strategic realignment of their processes not only improved efficiency but also boosted customer pay satisfaction.
These case studies highlight the importance of identifying and eliminating non-essential tasks in change management. By focusing on value added activities, businesses can enhance their processes, improve customer satisfaction, and achieve significant business improvement.